The Baltic Ace car carrier sank in 2012 with more than 1,400 cars on board after a collision with a container ship near the entrance of the main shipping lane leading to Rotterdam port. Sadly, the vessel sank in just 15 minutes claiming eleven lives. The wreck was recently removed.
In its largest ever salvage award the Dutch Ministry of Infrastructure and the Environment contracted Boskalis and its partner Mammoet Salvage for the wreck removal operation. Pieter van Vuuren, Operations Manager with Boskalis subsidiary SMIT Salvage and responsible for the removal of the Baltic Ace, explains.
Could you describe the wreck site and why it was important to remove the vessel?
“The Baltic Ace had just left Zeebrugge, Belgium, bound for Finland when it collided with the Corvus J container ship which was coming from Scotland. The incident occurred near the entrance of the North Hinder Junction, which is in the shipping channel around 40 nautical miles from the port. She lay on her side in the channel at a depth of 35 meters, and only 10-12 meters from the surface. She had some 540,000 liters of pollutants on board such as heavy fuel oil and lubricants and posed quite a threat to the environment. In addition, of course, there was also the petrol, oil, batteries etc. in the vehicles themselves. Furthermore, this is a very busy shipping lane so the wreck was certainly a hazard to vessels, given that it was so close to the surface. The wreck therefore was closely monitored by the Dutch and Belgian coastguard authorities.”
The flexibility of the salvage method chosen by the salvors gave us confidence that the project would be executed successfully. And they didn’t disappoint us!
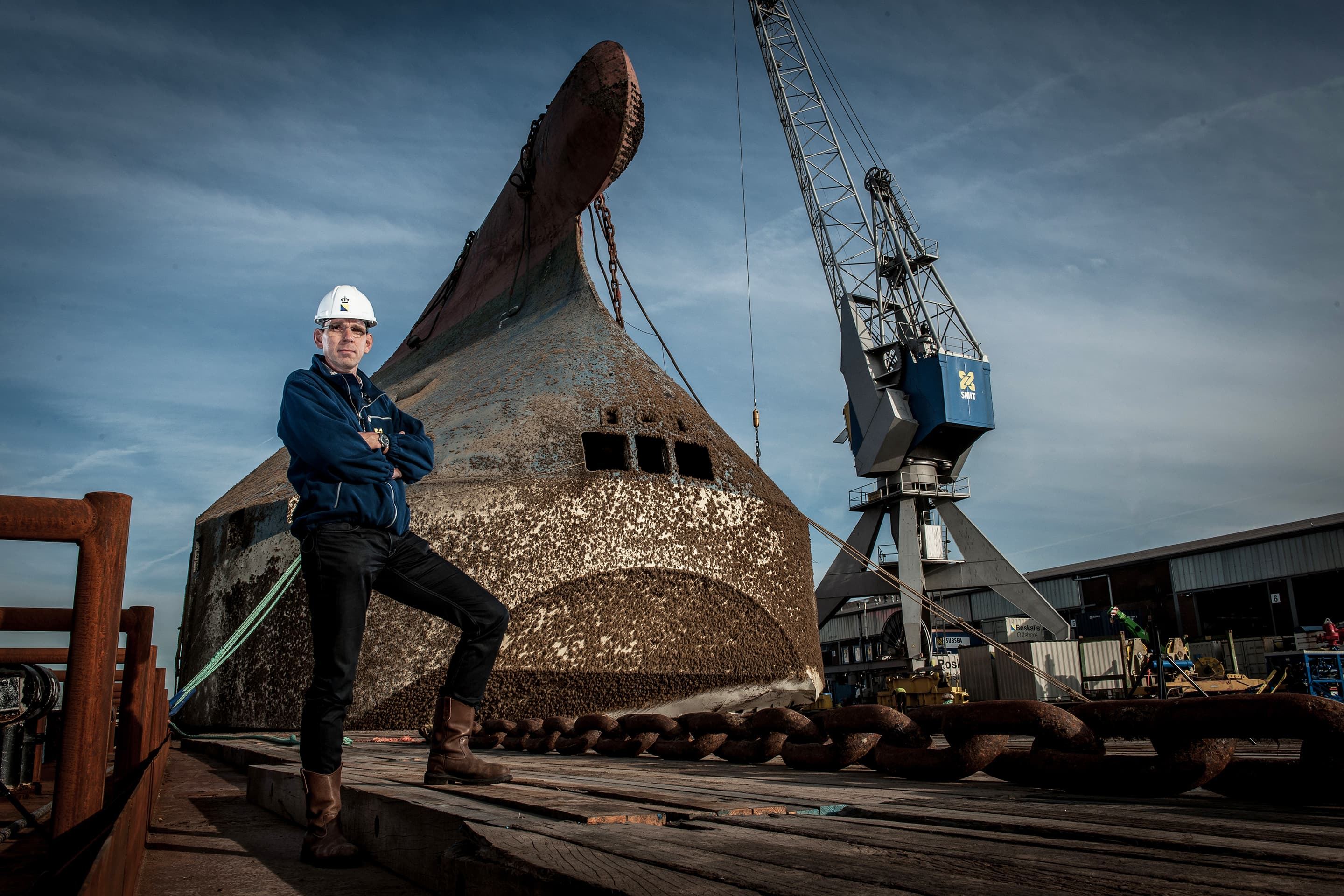
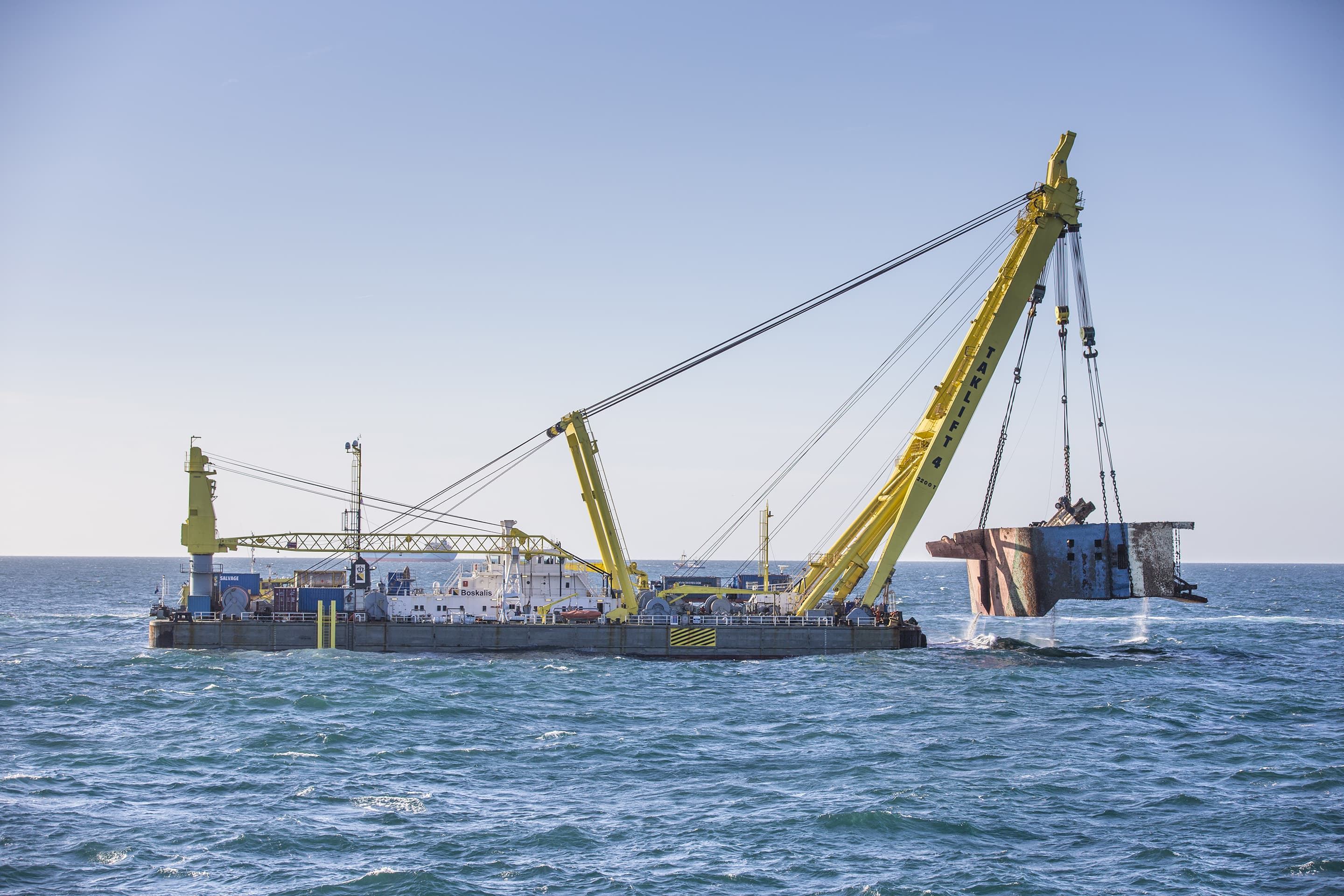
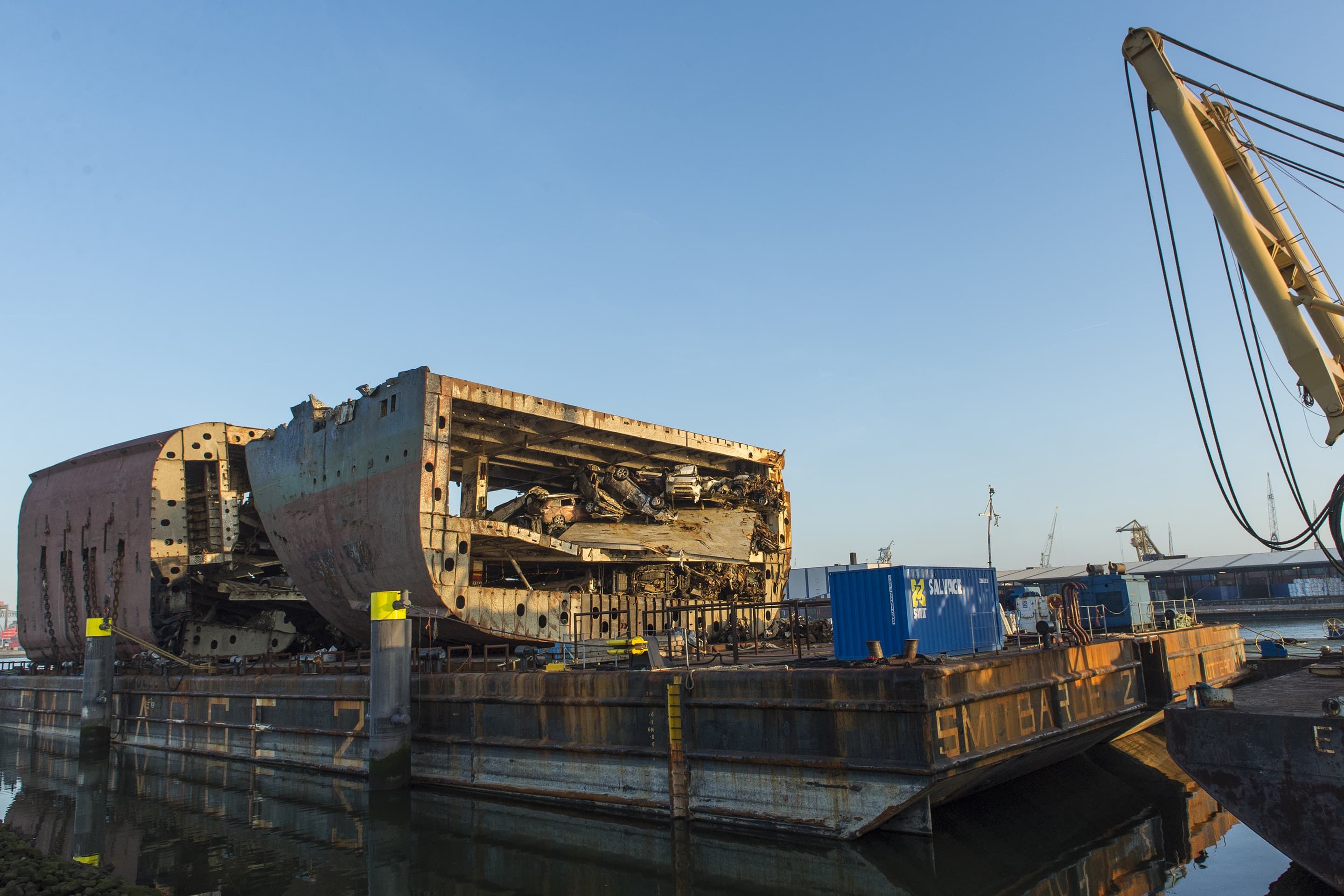
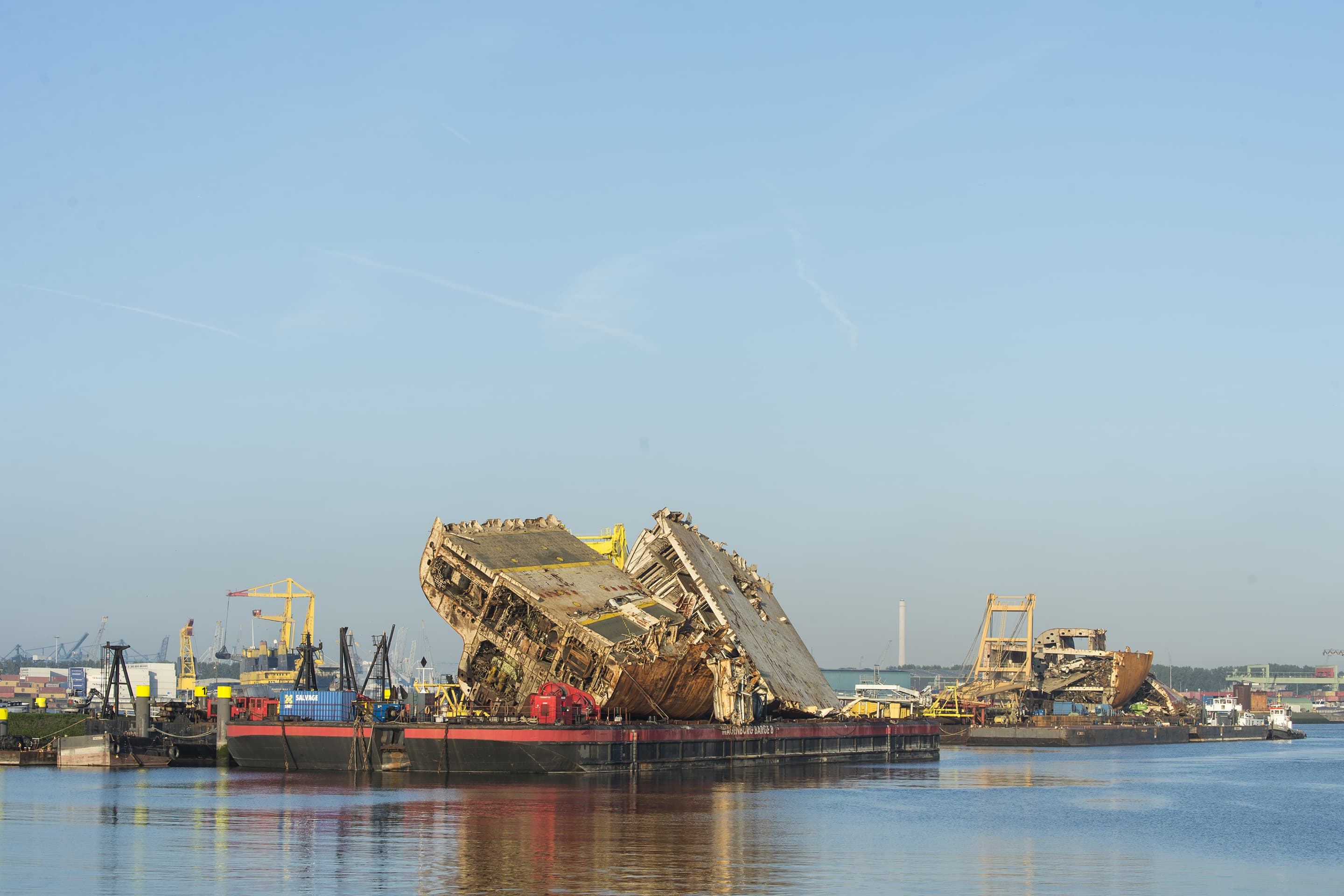
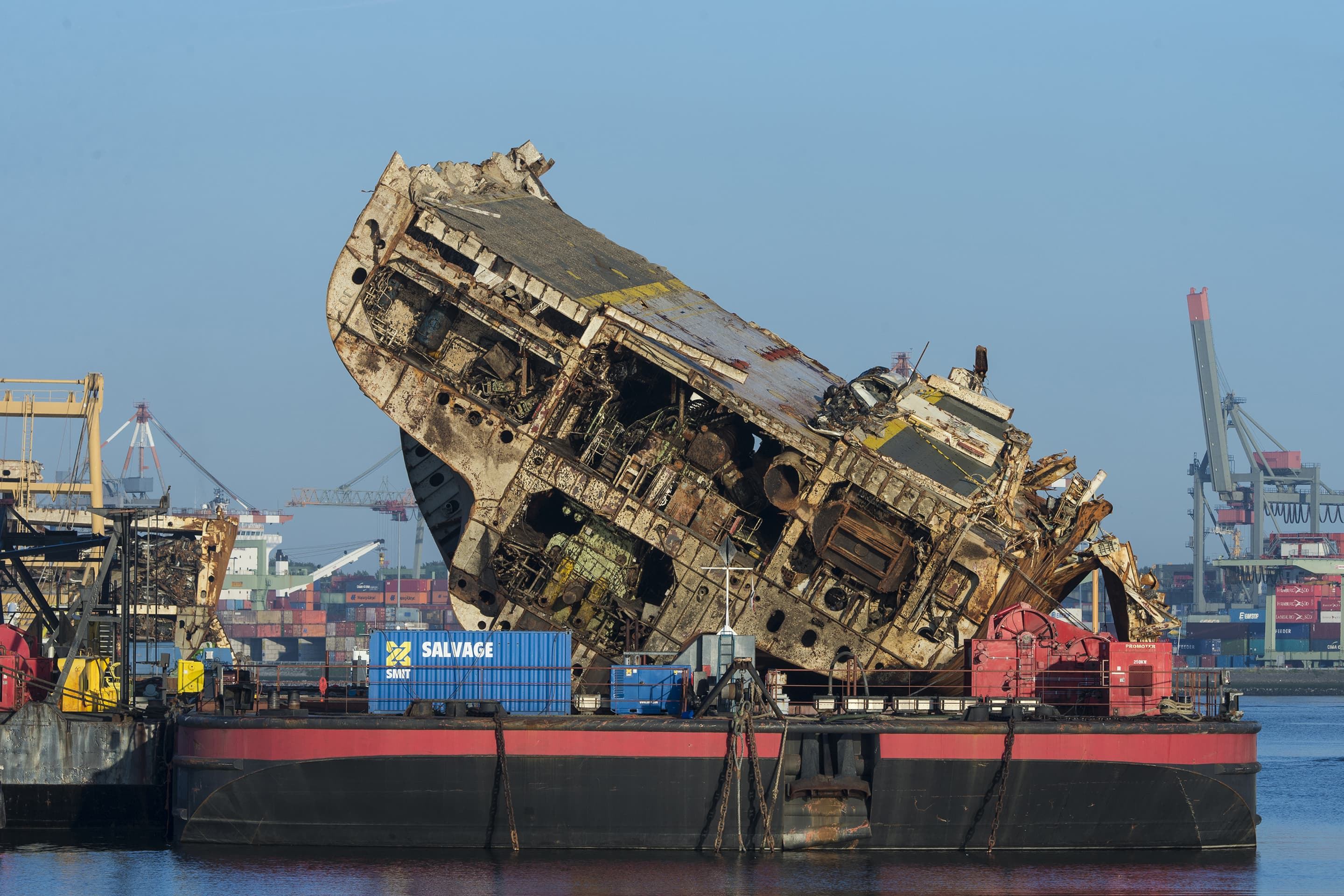
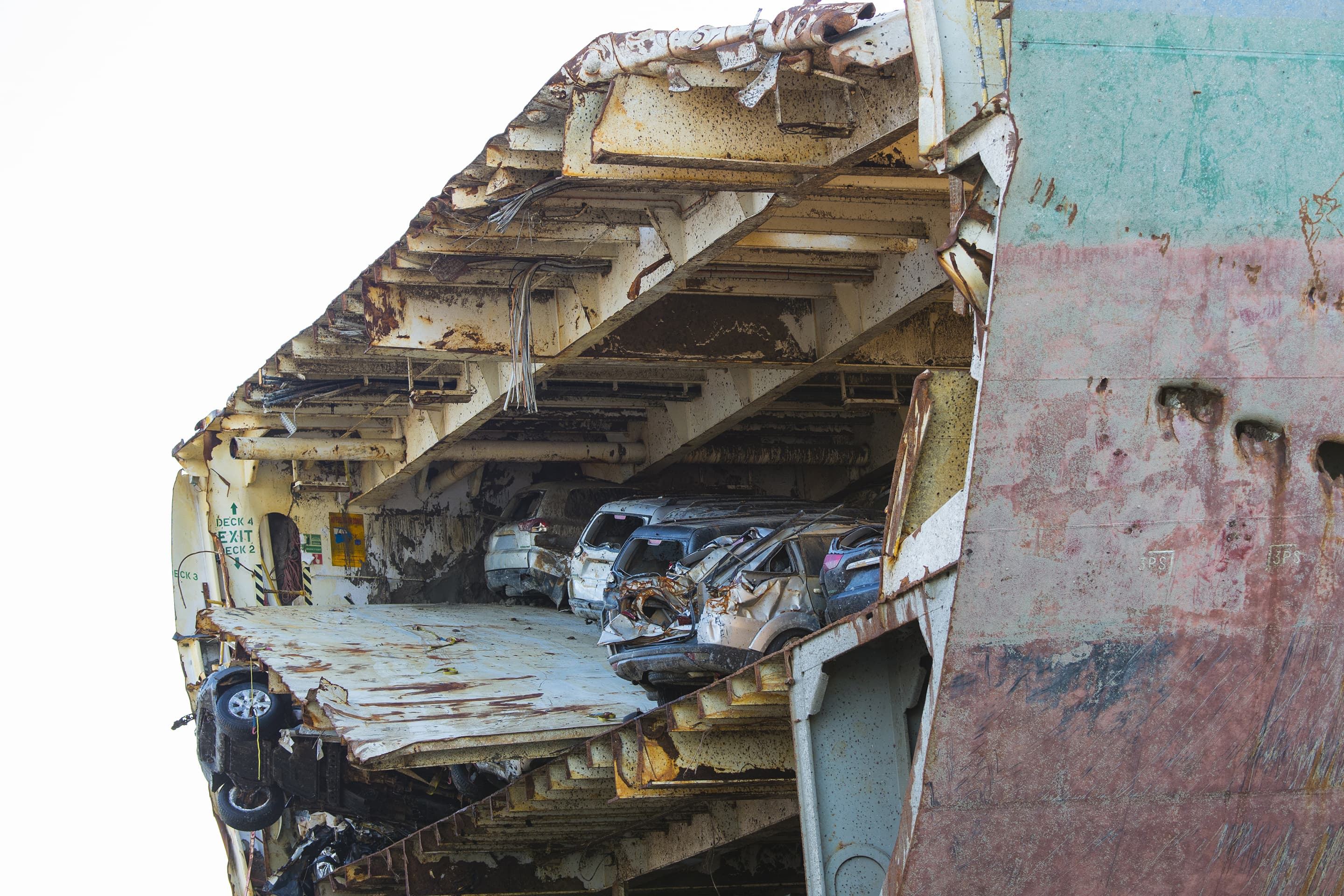
What was the scope of the contract and the equipment spread?
“Rijkswaterstaat (RWS), which is part of the Dutch Ministry of Infrastructure and the Environment, put out a tender for the vessel’s removal at the end of 2013. This required three plans from the contractor: the execution plan, a risk assessment and an environmental plan. For RWS it is currently quite common to contract on the basis of more than just price, but also taking quality into account. Boskalis has a lot of experience with these types of contracts, so with Mammoet we could submit a very concise proposal and were awarded the contract in March 2014. The activities included the removal of the entire wreck, its cargo and 540,000 liters of heavy fuel oil and lubricants.”
“Execution started in April 2014 and we are contractually obliged to complete before the end of 2015. Of course, in the North Sea it is usually only possible to work from April to September. We expected the removal to take two seasons. Our plan was to remove the oil in the first season in 2014 and remove the wreck from the seabed in 2015.”
To cut a section of 25 meters wide and 25 meters high takes around 30 hours.
Boskalis used its pioneering oil removal method and the majority of the fuel was pumped out in just a few days?
“Indeed, it is crucial to get the correct temperatures for optimum pumping of the various fuel oil grades. We used hot tapping with a heating system and developed this method to remove fuel from the tanker Kyung Shin which sank in Korea in 2010 and from the cruise ship Costa Concordia that ran aground off the coast of the Italian island Giglio in 2012. The oil is heated with inserts in the bunker tank. Steam is run through these inserts, which are cylinders of 2 meters long and 30 cm in diameter. The steam plant was installed on a barge and provided constant heating to create the flow of oil in the tank. We initially thought the oil would be pumpable in a couple of days but actually it only took 36 hours. By early June, 460 m3 of fuel oil had been removed from the tanks and was safely discharged. The tanks were also flushed three times with so-called super-heated water to remove all sticky remains.”
Following the oil removal, the next phase was preparing the wreck for lifting?
“Yes, from our survey during the tender stage it was quickly apparent that the vessel could not be lifted intact. Initially, we had decided to cut it into six sections of 1,500–2,000 tons each. The whole weight, including the cargo was 12,000–13,000 tons.
The Baltic Ace would be cut into pieces using a cutting wire. Previously, SMIT Salvage used a similar method during the salvage of the Russian submarine Kursk in the Barents Sea and of the car carrier MV Tricolor, which sank in the English Channel. To cut a section of 25 meters wide and 25 meters high takes around 30 hours. The sections are then lifted with large sheerlegs onto a barge and taken to a recycling plant.”
I also think this shows how different boskalis business units share their knowledge to arrive at safe, efficient and cost-effective solutions.
However, not everything went according to the initial plan?
“No, we had to adapt the first plan. For the lifting preparations we had to cut holes in the ship’s hull to insert the lifting saddles or bollards. We do that to create strong points in the vessel to cope with the lifting forces. But when we went to start cutting the holes we could see that the ship was deteriorating rapidly — frames were breaking and coming loose. Our highly experienced Salvage Master could see the initial plan was not going to work. We had to go back to the drawing board and design a fresh plan. This time we decided we would still cut the Baltic Ace up but it was necessary to make more sections.”
“Given a car carrier’s square shape, all the strength is in the lower deck up to around the 4thor 5th deck. The new plan involved eight sections instead. We would lift the keel up to deck 4 and then use the wreck grab for the upper decks and smaller parts on the seabed. For the cutting spread, the Baltic Ace was slightly different to the Tricolor when a jack-up barge was used. This time, we wanted to use barges with a heave compensation system. The pre-tensioned saw-wire (80 meters-120 meters), which has steel ‘bushes’ — with sharp bits of hard metal on the outside — along it, is pulled up and down by wire winches between the barges. Mammoet has developed an in-house horizontal drilling system and after drilling they pulled the wire underneath the wreck. In a constant hauling and heaving motion, it took 30 hours for each cut. We started in April 2015 and by the end of May, the vessel was cut into eight sections.”
“By using the floating barges for cutting the wreck, we are reinventing the principles and developing an automated cutting process. This really shows our collective expertise and how we can draw on synergies from different parts of the Boskalis group. For example, the heave compensation system was designed based on a system used for dredging and now it has been introduced into the salvage arena.”
“By the end of September the sheerlegs had loaded eight sections and some 5,000 tons of smaller parts with the wreck grab onto four barges. The barges were then taken to a nearby recycling yard in Vlaardingen. We experienced some delays because of the weather but the client knew we were doing our utmost to effectively do the job.”
Boskalis has also been tasked with cleaning the seabed?
“The seabed has to be delivered in the cleanest state possible and we are using the grab to retrieve the smaller parts off the bottom. Divers will clear any remaining waste.”
Looking back on this successful operation as the Operations Manager, what are your thoughts?
“This project shows how different Boskalis business units with their own unique expertise come together and share their knowledge to arrive at safe, efficient and cost-effective solutions. We completed the project well before the deadline.”