The construction of the new Suez Canal marks a milestone in maritime history and was unprecedented in terms of speed, manpower and equipment. And even though it was a race against the clock to keep it on schedule, this huge undertaking was achieved successfully — on time and within budget. In only ten months the new Suez Canal was ready.
On 5 August 2014, the starting signal was given for the new Suez Canal project. The project was originally scheduled to take about three years to complete. However, the president of Egypt, Abdel Fatah al-Sisi, stipulated that the works were to be completed in exactly one year. This made the project extremely challenging. Boskalis, in consortium with partners, was responsible for the construction of a new 35-kilometer section that pushed the boundaries of the industry. Boskalis colleague and Project Director of the Consortium Jaap Dekker led the Challenge Consortium. Together with other members of the vast Boskalis team he reflects on this mega-project, in which there were days when more than 1.4 million m3 of sand was dredged. In a trial run the first commercial ships were able to pass through the new canal on 28 July 2015, a week ahead of its official 6 August opening.
Jaap, how did the project start?
“Well, tendering started in August and September last year. Large projects of this size normally take years of preparation rather than just months. Tender results were made public at the end of September and just two weeks later, by mid-October, the contract was awarded to the Challenge Consortium. The Consortium was responsible for the construction of a 35-kilometer-long parallel canal, 147 meters wide and 24 meters deep. The Challenge Consortium comprised the National Marine Dredging Company from Abu Dhabi, Jan De Nul from Belgium and Van Oord and Boskalis from the Netherlands. Initially, it was quite a job to sort out the differences between the partners in terms of the meeting culture, working methods and safety programs. So it’s not surprising that we adopted the name ‘Challenge Consortium’ during the tender phase. This project has been a challenge from start to finish. However, the time pressures did have an advantage: the tight deadlines put the squeeze on bureaucracy and endless discussions. That helped maintain the pace that was necessary.”
In just nine months, we moved a volume of sand that was the equivalent of eighty great pyramids of gizeh. that is absolutely unprecedented!
The mobilization period was also quite exceptional?
Jaap: “Yes, it has been a completely unique project in every respect. The speed at which we managed to mobilize the largest dredging fleet ever without any time for preparation is unparalleled. In total 21 cutter suction dredgers and 5 trailing suction hopper dredgers were deployed, as well as two water injection dredgers. While coordinating the dredging fleet was a gigantic operation, an even greater challenge lay in mobilizing all the auxiliary equipment, such as 80 kilometers of pipelines, and organizing the logistics and installation of everything needed to allow the dredgers to get to work.”
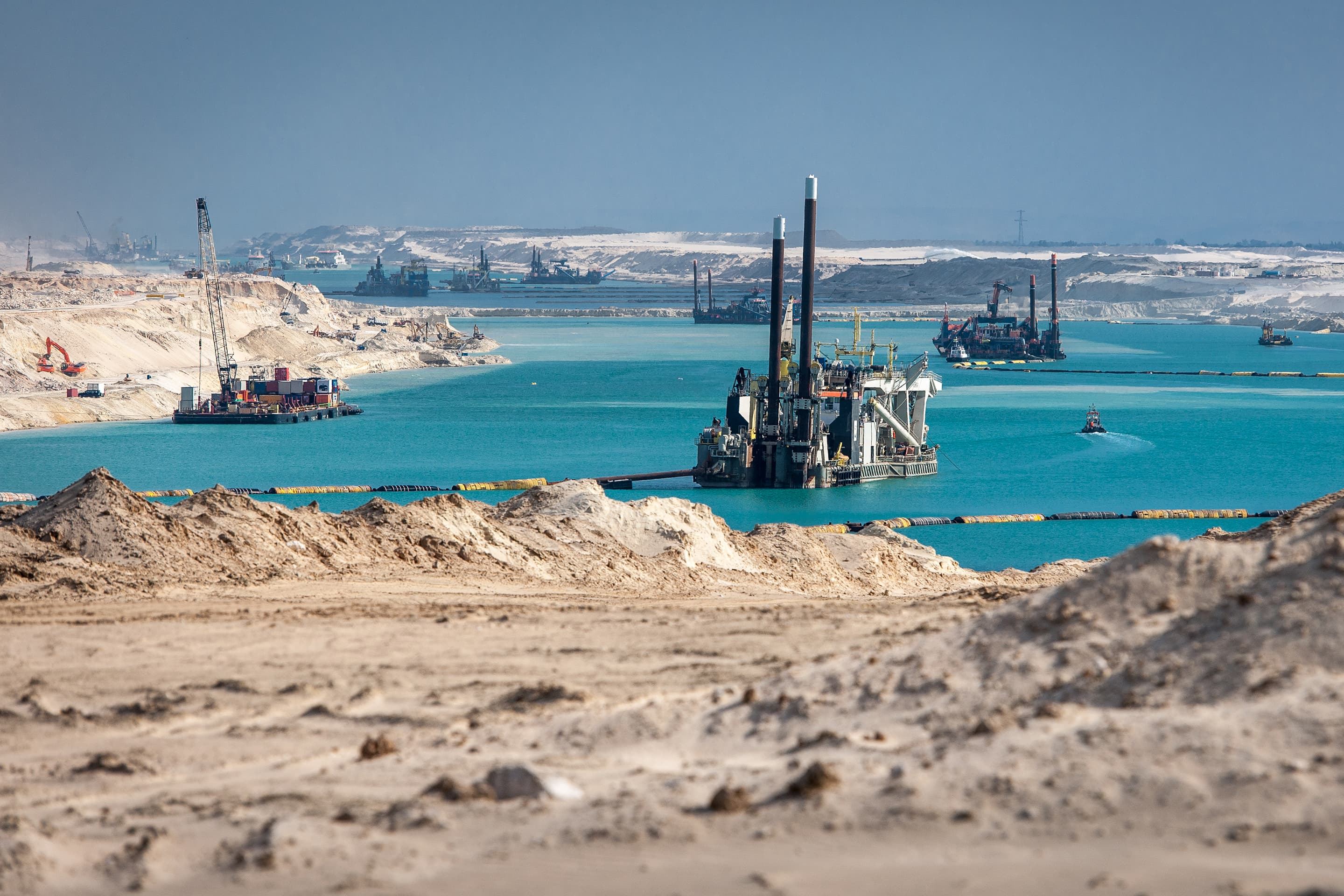
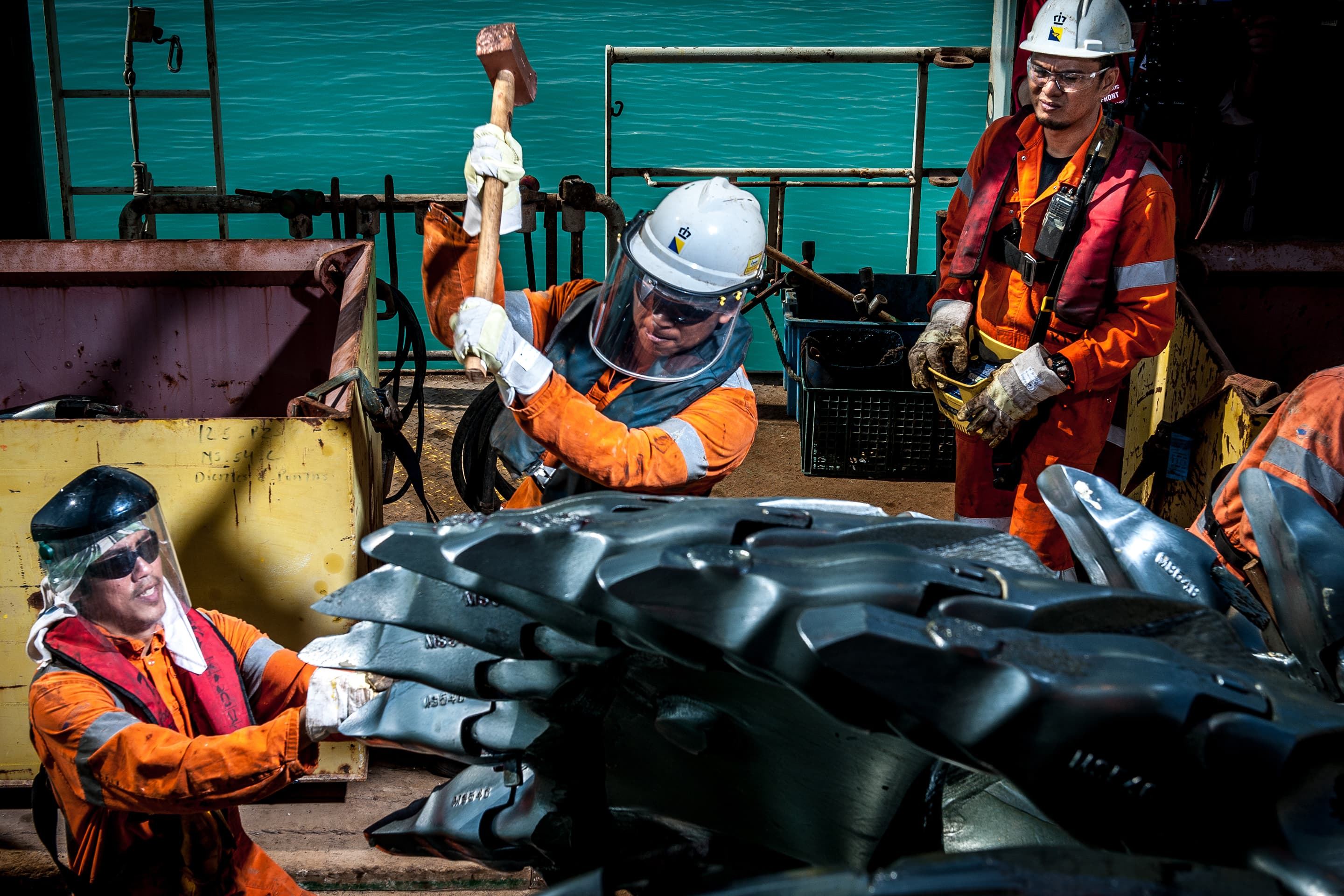
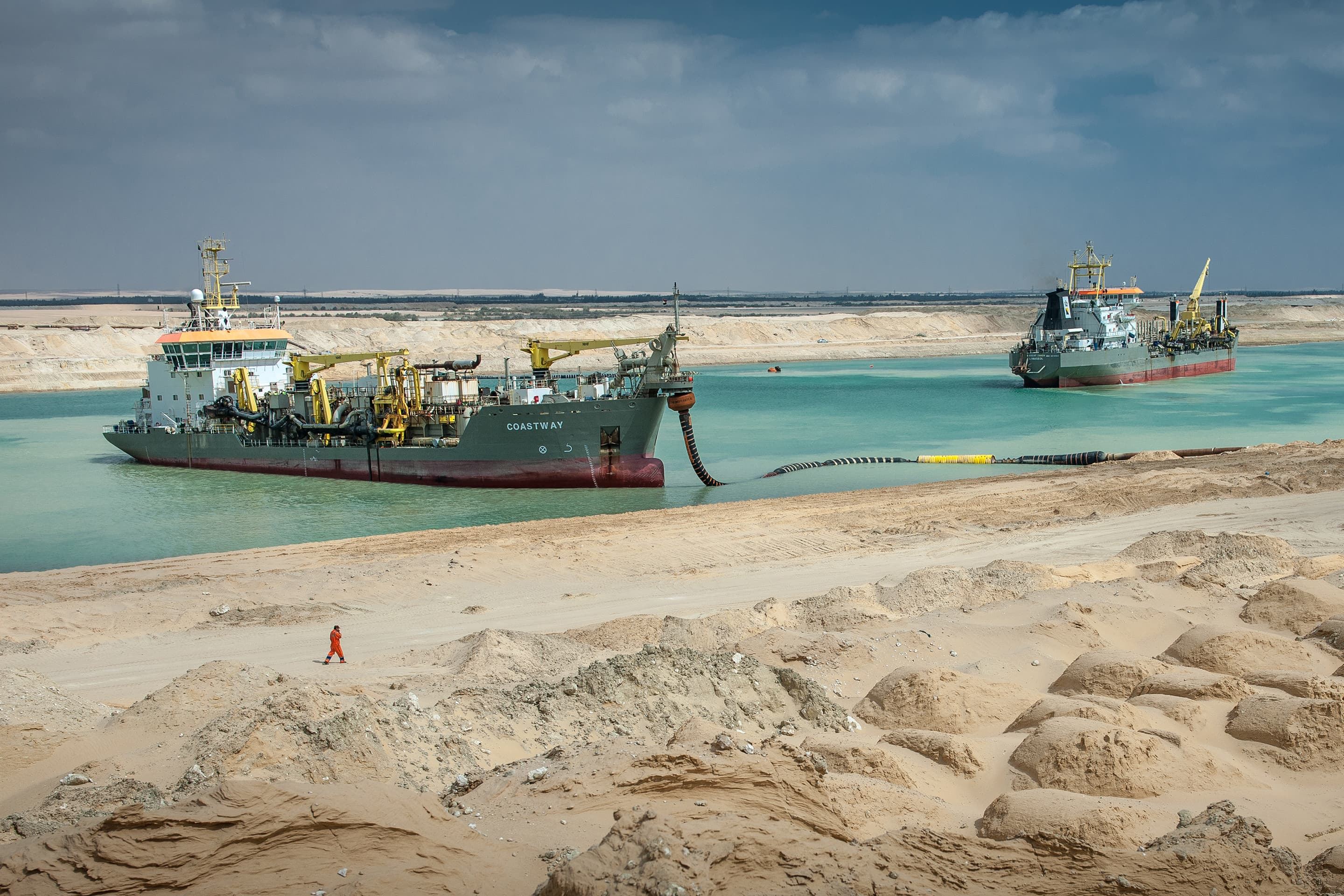
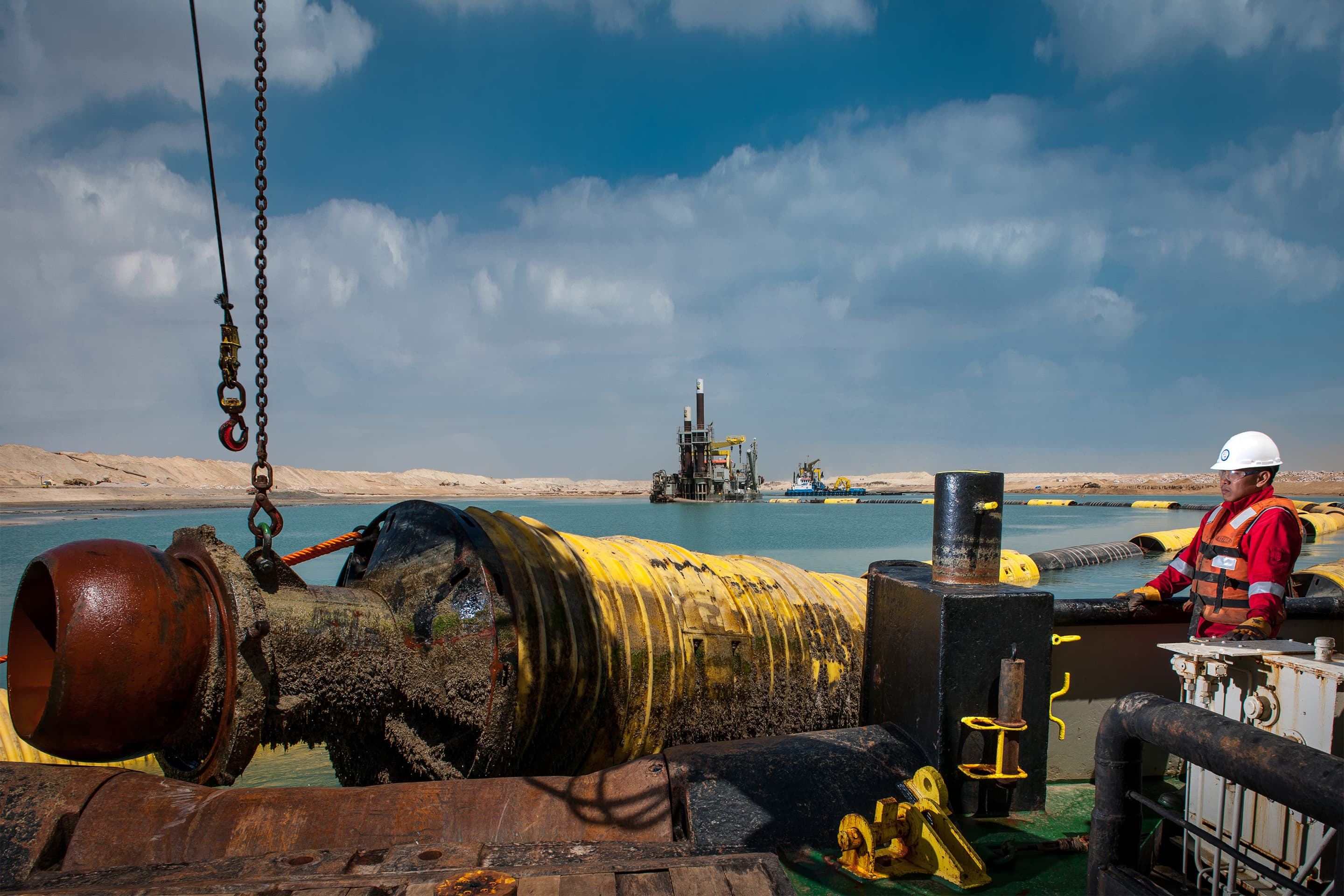
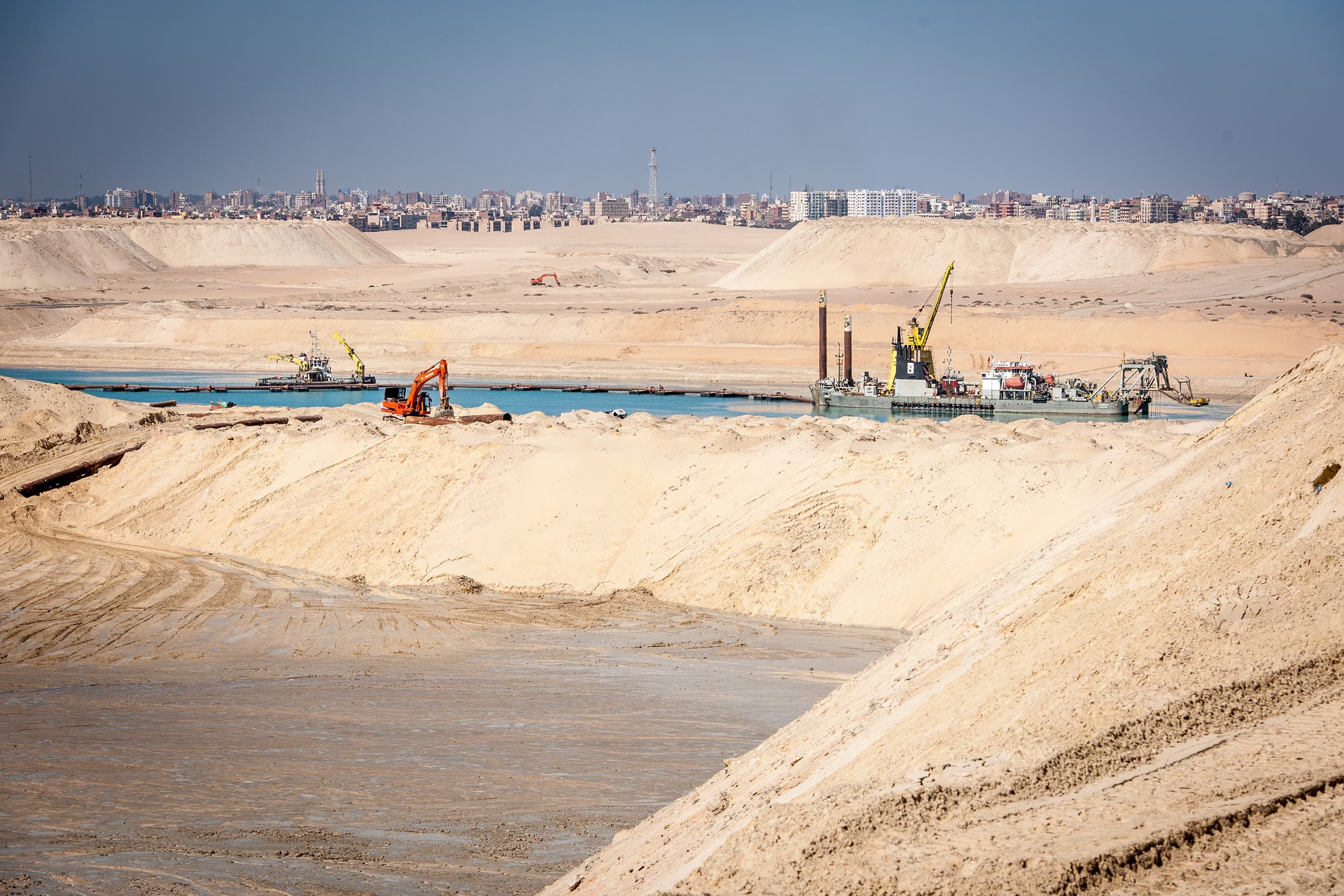
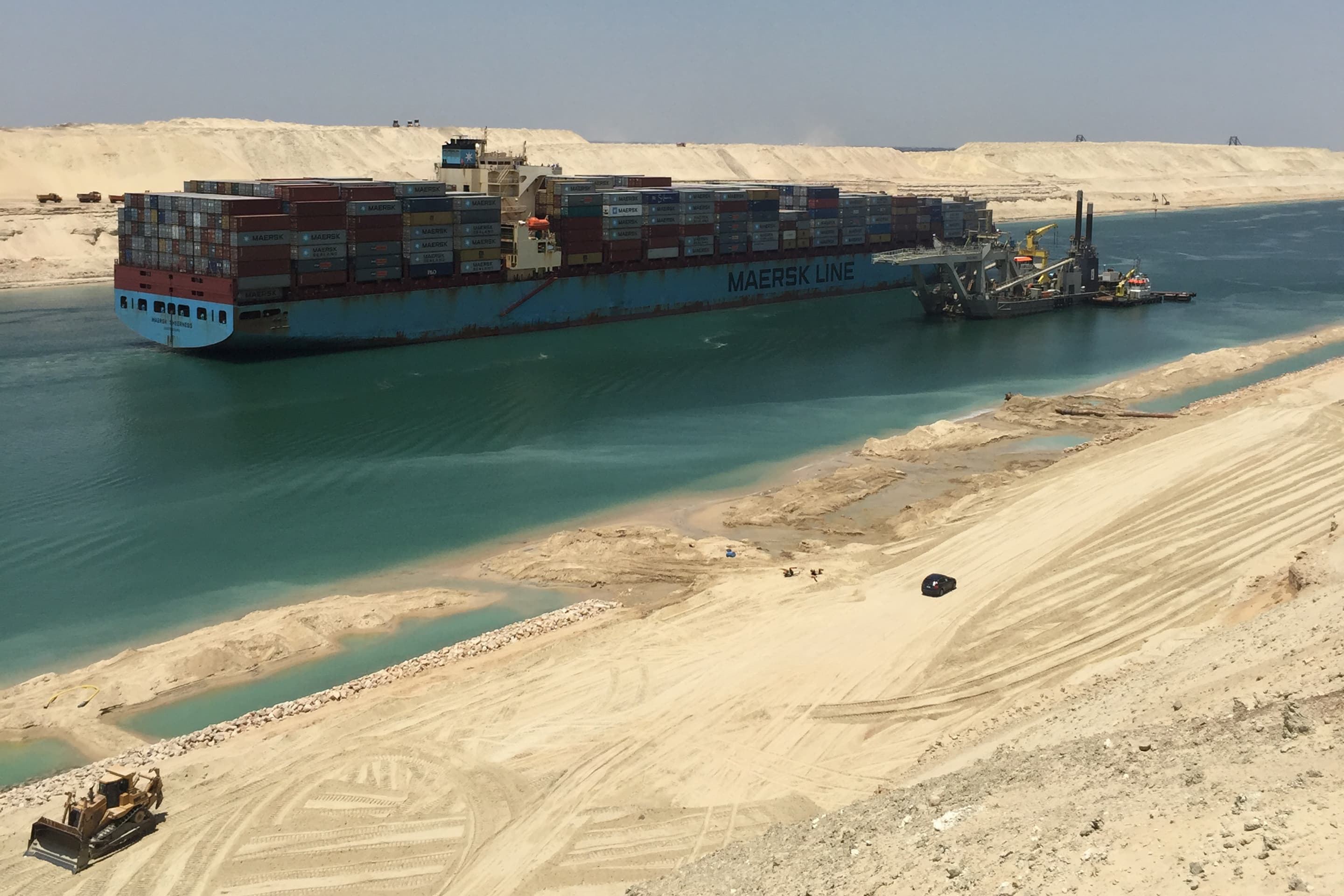
The new Suez Canal was of such a mammoth scale, how was the project organized Gert-Jan?
Gert-Jan Peters, one of the project managers: “Given the length of the new parallel canal, the work was divided between four sub-organizations, each of which was responsible for one section. We were working not only with our own vessels, but also with cutter suction dredgers from the consortium partners.”
Each project is unique, but the size and the speed of this one put it into a league of its own! this really was a ‘once in a lifetime’ project.
“The planning for the ships was a complex puzzle. The trick is to use the right equipment in the right place, taking the various types of soil and the maximum dredging depth of the smaller dredgers into account. This meant that work was going on in 10 areas at the same time. That was the only way we could achieve the required production volumes.”
“It was a bonus that, in some sections of the planned route, the bed contained more sand than expected. In those locations, we were dredging to a depth of 8 meters as quickly as possible with cutter suction dredgers and creating turning basins with shore connections on either side. Once that was done, we could start working with trailing suction hopper dredgers at those locations. Deploying different types of equipment improved productivity and saved a lot of time.”
We have accomplished something altogether unique. I will probably never be involved with a project of this size ever again.
And even pyramids presented a major challenge — but not the ones we usually associate with Egypt. Is that right?
Jaap: “Yes, ironically. One of the main challenges was the operational monitoring. Local contractors working for the army were doing the dry earthmoving and excavating the planned route down to sea level. But this produced enormous mountains of sand on either side of the Canal, sometimes as big as 200 meters wide and 40 meters high. These so-called ‘sand pyramids’ not only made drainage difficult on the sandfill, but the steep slopes also made it very difficult for the people in our sandfill teams to install the 80 kilometers of pipelines required to remove the dredged material. As soon as the local contractors gave the go-ahead for a particular section, we made sure that the sandfills, pipelines, landfalls and drainage were ready, and immediately started on the pre-dredge surveys that were required before the cutter suction dredgers could start work. We were using the Boskalis survey system and so most of the survey work on the project was being done by Boskalis surveyors.”
The early stages of the suez project were a logistical challenge. we worked flat out on organizing more than fifty large transports with twenty dredging units, kilometers of pipeline and a vast quantity of smaller equipment.
And what was the atmosphere like amongst all the people at work?
Gert-Jan: “Our sub-organization consisted of all sorts of people who had never worked together before. Some 45 nationalities were at work on the project. Because everything started so quickly and because of the enormous amounts of equipment and people arriving in Egypt in such a short space of time, things did look chaotic at times. But despite all the rush, and the different backgrounds and company cultures, we achieved good results. The number of people working here quickly rose to about 2,000. For a workforce of that size, accommodation and transport alone represent an enormous logistical operation.”
“And as for the atmosphere: everybody was very impressed by the size of the project: we all had the feeling that we were working on something unique. The views weren’t particularly impressive — just sand as far as the eye could see. But it was a real candy store for our vessels. With all that sand, we could really pump up production and that certainly gave us a kick!”