Dozens of wind turbines, standing meters tall, generate green electricity at sea. But how does this wind energy reach homes and companies on land? Precisely: through thick (export) cables. In 2024, Boskalis installed two 64-kilometer-long export cables for the offshore wind farm Hollandse Kust West Beta in the Netherlands. And impressive equipment was needed for this.
With an average height of about 5 feet 11 inches, the colleagues on the beach at Wijk aan Zee were not the smallest people in the world. However, they paled in comparison to the white, 72-foot-tall burial sledge BSSIII set up on the beach. A few dozen meters further into the North Sea waters was the Giant 7: a 450-foot-long vessel equipped with a crane capable of lifting up to 1,000 tons. The scene immediately illustrated the scale familiar to offshore colleagues but entirely new to the average Dutch citizen on land: installing and connecting an offshore wind farm to the local power grid requires enormous vessels and structures.
What visitors couldn’t see was the meticulous preparation that preceded the offshore execution in the North Sea. Over two years were spent calculating every detail of the activities involved in a cable installation project. Despite appearing robust at 10 inches thick, the export cable for the Hollandse Kust West Beta project is surprisingly fragile. “A cable is inherently delicate and has its limits – strict limits, in fact,” says project director Bart Roeleveld. “The cable designed for this project has restrictions on the tonnage pull and the angle it can endure during installation. We adhered rigorously to these parameters because failing to do so risks damaging the cable. That extensive calculation work was critical to the project’s successful execution.”
One chance
Thus, a relatively subtle pulling operation took place off the coast of Holland from the Giant 7. The crane vessel was equipped with a load tower, a carousel, and the burial sledge BSSIII. Project manager Radboud Stelling explains, “Landing the cable on the beach is the biggest challenge in this type of project. You only get one chance to do it right; there’s little to no room for error. The combination of the Giant 7 and the BSSIII performed exceptionally well, successfully burying the first 2.5 miles of the export cable at a depth of 26 feet.”
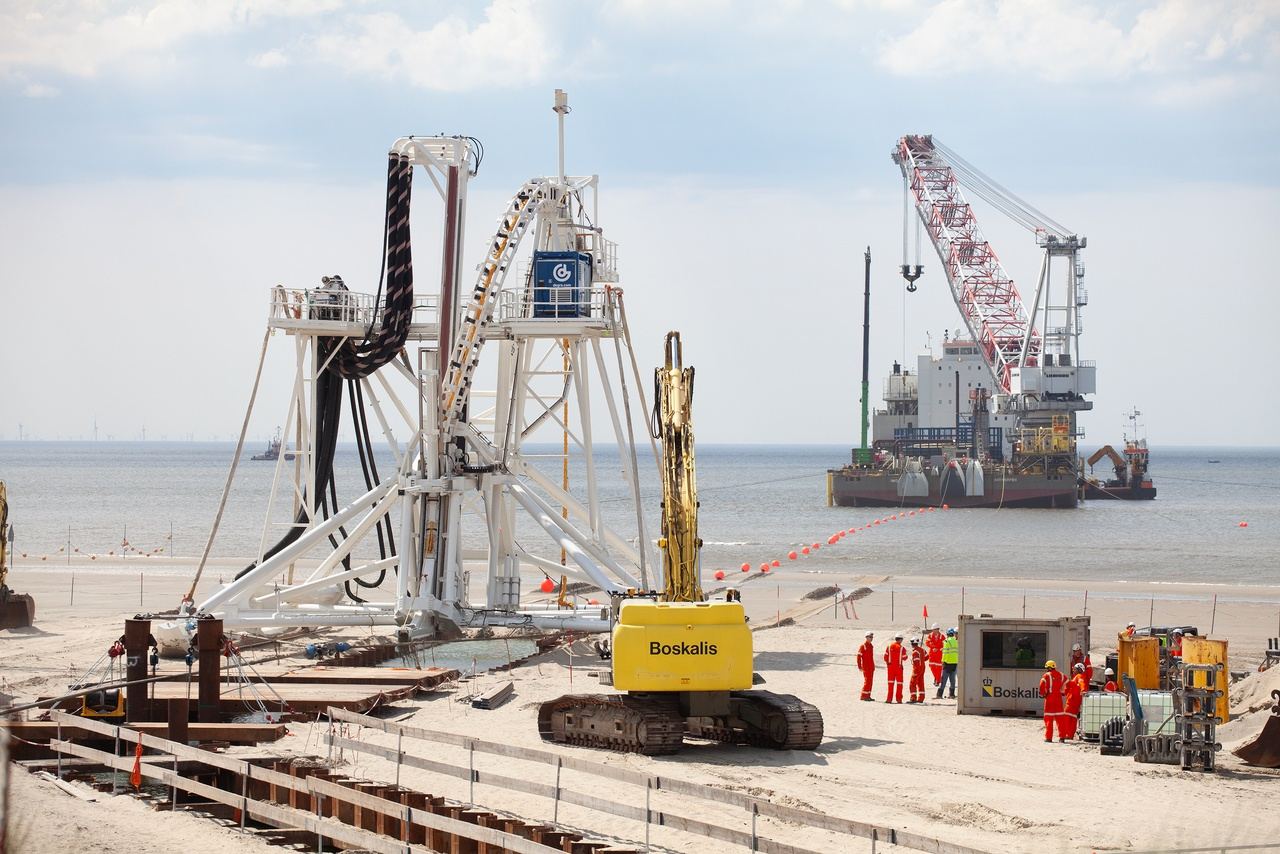
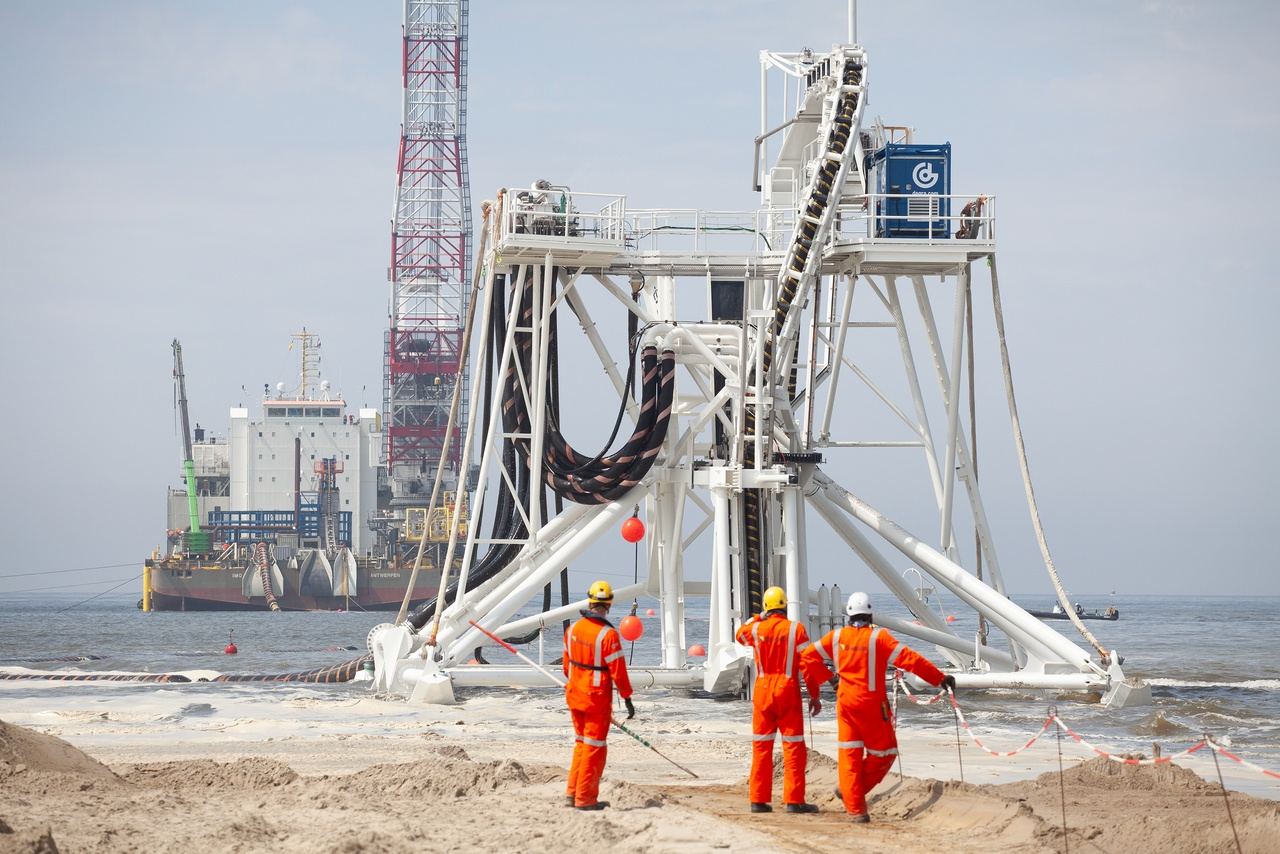
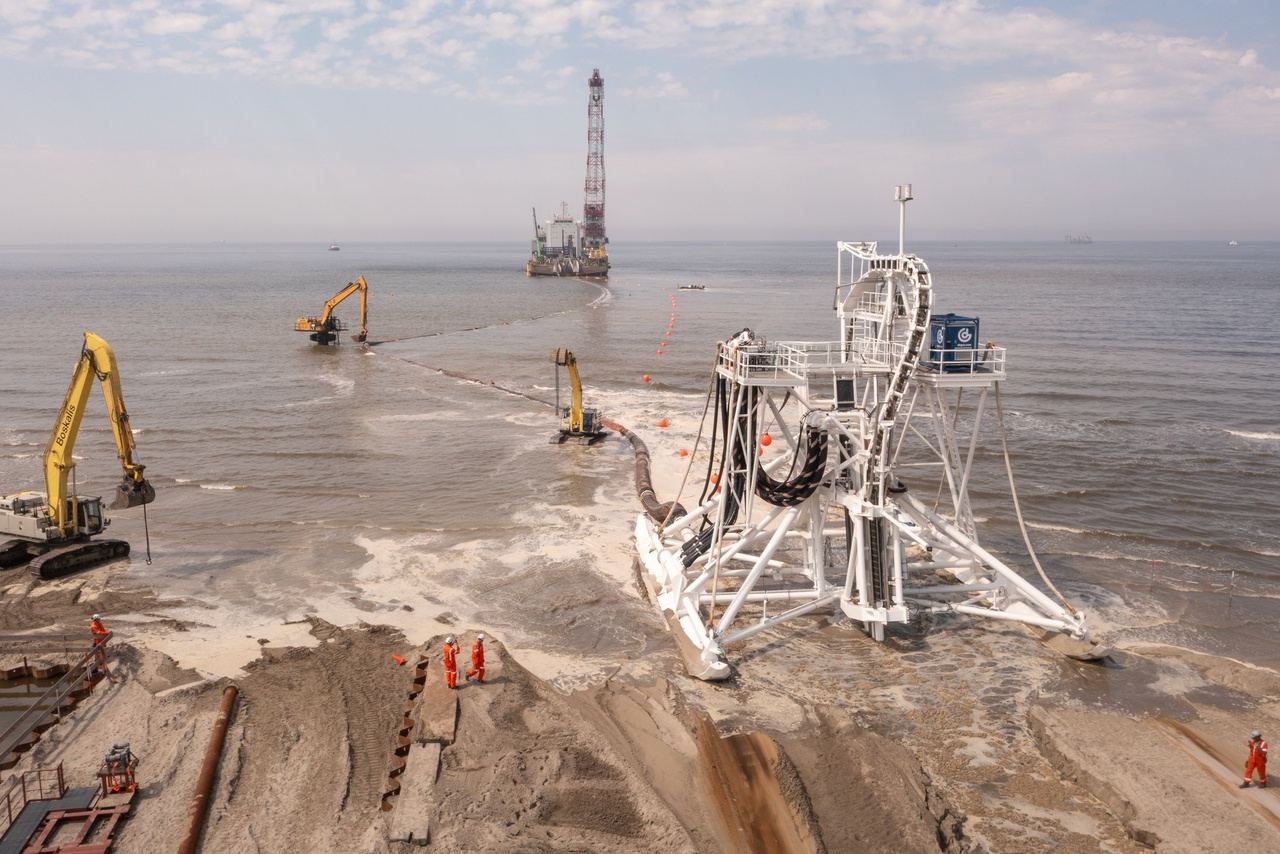
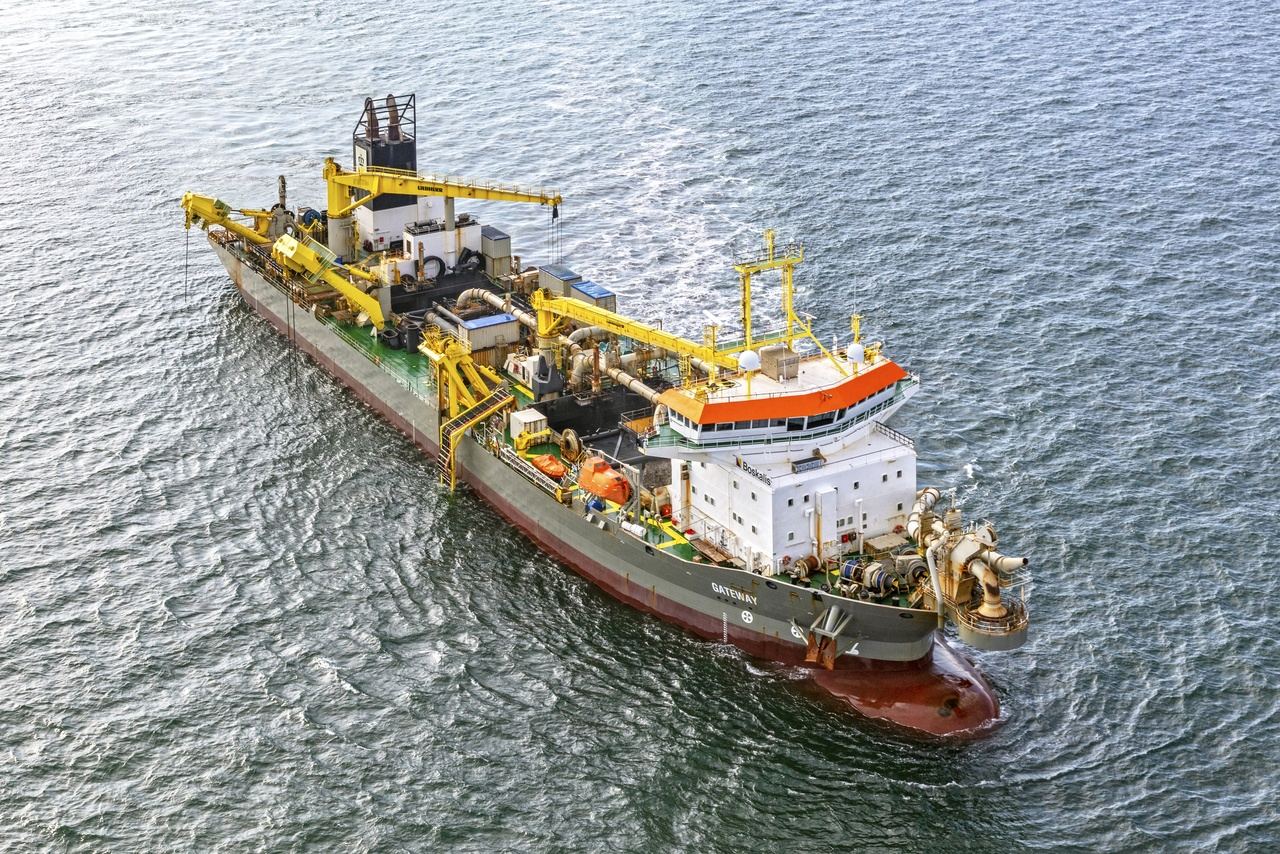
Where the nearshore section of the cables ends, the much longer offshore part begins. For this, Boskalis deployed the cable-laying vessel Ndurance, after which the Ndeavor buried the cable under the seabed. For the offshore portion, the two export cables were divided into four sections, three of which were identical in length. This division was precisely calculated beforehand to minimize installation time, Stelling says. “Because three of the four offshore cable sections were exactly the same length, it didn’t matter during installation where each section was placed. This flexibility allowed us to adapt during execution. If we couldn’t install at one location, there was always the option to switch to another part of the cable route.”
Tying them together
The separate cable sections also had to be connected. This was done aboard the vessels. “We used both the inline joint and the omega joint,” says project manager Jochem van den Bosch, responsible for offshore cable installation. “With the first technique, cables are spliced end-to-end aboard the vessel. This involves retrieving one cable end from the seabed and connecting it to the next cable on the carousel. The omega joint, on the other hand, involves retrieving both cable ends onto the vessel and splicing them in the shape of the Omega symbol. This shape is necessary to prevent the cable from bending too much.”
On the beach, visitors and beachgoers closely observed the operations. Roeleveld: “It was fantastic to work so close to shore and give people a chance to see firsthand what goes into installing a cable. It made our offshore work more tangible, especially compared to installing cables between wind turbines within a wind farm. It’s great that the Netherlands could witness what Boskalis is capable of. This achievement is thanks to the many experts at Boskalis Subsea Cables, who bring a wealth of experience, including from the Borssele project. This strengthens our impressive track record.”