As the new, self-propelled crane vessel cuts its teeth on its first offshore wind project, Gerben Swan, captain of the Bokalift 1, and Rick Maliepaard, Fleet Management Director of the Boskalis Offshore Energy division, tell us why this vessel is in a class of its own.
The Bokalift 1 is more than ‘just a crane vessel’, isn’t it?
Gerben Swan: “For sure. It’s not the 3,000-ton revolving Huisman crane that makes the Bokalift 1 unique but the whole concept – a powerful crane, a 7,000 m², unobstructed deck, all combined with dynamic positioning capabilities (DP2) and an anti-heeling system. It opens up opportunities for Boskalis in a new sector of the heavy lift market.”
Rick Maliepaard adds: “The concept – the crane with the large deck of 165 meters by 43 meters and the integrated systems – is fundamental. We can transport everything on deck so we aren’t dependent on barges, which have substantially lower workability.”
And this is the first DP2 crane vessel in the fleet?
Rick: “In the past, we used anchor spreads to deploy heavy lift equipment on offshore installation projects. This is our first DP vessel with a powerful rotating mast crane and an anti-heeling system. Due to the DP2 capabilities for dynamic positioning we don’t lose time on the anchor spread deployment.”
Gerben: “The vessel can handle more than 60 knots of wind on the bow and winds of force 6 to 7 on the beam, and the vessel can maintain its position in strong currents.”
Which markets is the Bokalift 1 designed for?
Rick: “This is a very flexible vessel and it is well-suited for transport and installation projects on offshore wind farms, oil and gas fields, and salvage projects. It is already proving herself in the offshore wind industry at East Anglia ONE with the successful installation of turbine foundations. The next projects will be in the oil and gas sector: the decommissioning of the Viking and Vulcan platforms for ConocoPhillips in the Southern North Sea, and the L10-AD platform, which was the first platform to be positioned on the Dutch continental shelf in 1972. The Bokalift 1 can also transport and install newbuild production platforms and assist on complex wreck-removal projects.”
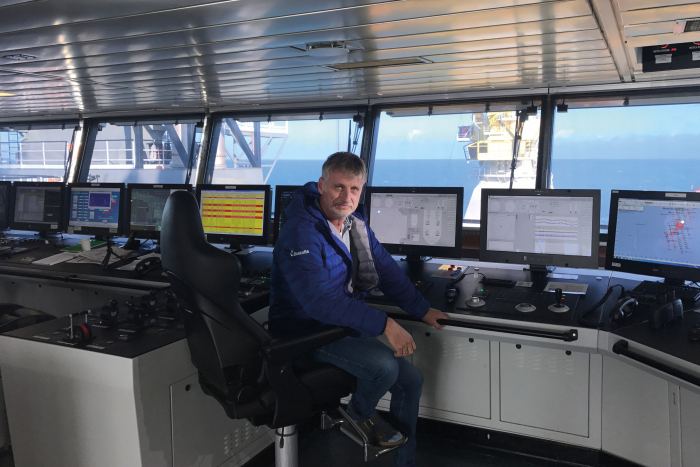
Gerben Swan, captain of the Bokalift 1
Can you outline the activities the Bokalift 1 is carrying out at the East Anglia ONE offshore wind farm?
Gerben: “We started work at the wind farm in April 2018. The location is in the southern section of the North Sea around 60 miles off the UK coast. This is a large wind farm and we are working with the Bokalift 1 for Van Oord on piling and jacket installation at 102 locations.”
“First, we lower a specially designed template to the seafloor to guide the piles into the seabed. This is a big job in itself: the template weighs some 580 tons. Once it is in position, we stab the piles into the seafloor and then use the hydraulic hammer to pile them to the required depth. We have to hammer three piles to the correct depth at each of the 102 locations. We then remove the template and the location is ready for the jacket installation, which can take four to five hours.”
Rick: “Because of our broad range of services, we are not only involved in the installation of the foundations for this wind farm. Boskalis is also transporting the jackets from the production yard in the Middle East to the port of Vlissingen in the Netherlands, where they are loaded onto the Bokalift 1. And we are laying the 102 inter-array cables that connect the wind farm’s turbines.”
THE CONCEPT – THE CRANE WITH THE LARGE DECK OF 165 METERS BY 43 METERS AND THE INTEGRATED SYSTEMS – IS FUNDAMENTAL.
East Anglia ONE highlights the importance of the vessel’s integrated concept, doesn’t it?
Gerben: “Absolutely the integration of the crane in the concept as a whole is crucial. We are working with dynamic positioning and an anti-heeling system. With every movement of the crane, the anti-heeling system responds by triggering eight big ballast pumps and compensating for the expected list. The DP system keeps the vessel in position on the heading required. And the concept is certainly proving its worth on this project. We are working 24/7 with a staggered watch schedule.”
Rick: “We also demonstrated the flexibility and capacity of the Bokalift 1 by transporting two jackets on board of 900 tons each, the template of 580 tons and some 30 piles, which are usually 150 tons each on average.”
Gerben: “Essentially, we can stay out at sea much longer and there is less transportation involved, as well as fewer support units around the vessel. With DP2, the vessel doesn’t require anchor spreads and consequently we don’t need anchor handlers or barges.”
Were there any specific challenges during the project?
Gerben: “Although the seabed itself is sandy, the southern section of the North Sea is known for its strong undercurrents. That can be challenging, particularly when working with the Remotely Operated Vehicles (ROVs) we use for guidance and data acquisition during several stages of pile or jacket installation. In areas with strong tidal currents, it is advisable to consider options that make installation less dependent on ROVs.”
“Even so, considering this is the first project with the Bokalift 1, and that the crew had to familiarize themselves with the new vessel, I think we can be proud of where we stand.”
Rick: “We are also collecting data from 300 points on the vessel to assess her behavior. These data help us to look continuously for any improvements so we can enhance the vessel’s efficiency even more on subsequent projects.”
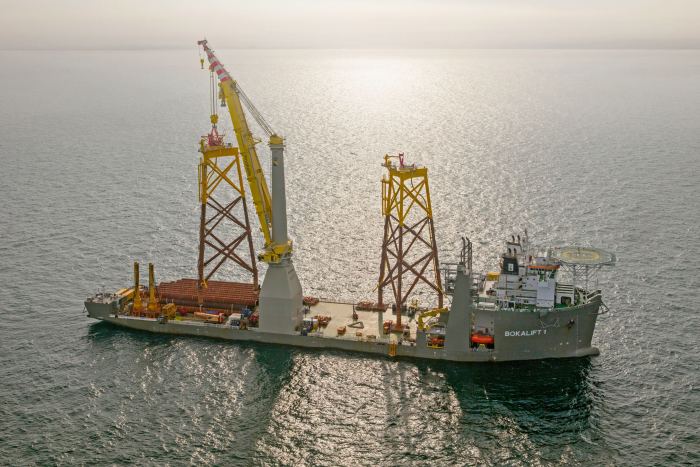
Why did Boskalis opt for such a large crane?
Rick: “Versatility is the name of the game in our industry. This crane gives us all sorts of options for lifting a range of objects, including oil and gas platforms. And turbine foundations are getting bigger in the offshore wind sector. During decommissioning work, the Bokalift 1 can remove a complete 3,000-ton topside and store it on the deck. On the Vulcan decommissioning project, we will cut the platform into five sections, all of which we can carry on our own deck at the same time. And we can take components from manufacturing facilities in Europe to an offshore installation project in Brazil, for example.”
Given the size and stability of the Bokalift 1, are alternative sea-fastening methods being considered to make offshore operations even more efficient?
Rick: “Yes, instead of full seafastening we can perform semi-seafastening for decommisioning projects. Rather than spend twelve hours on full sea-fastening, we may be able to transit back to base straightaway once we have the structures onboard. That saves a lot of time. Obviously, we can only do that when all conditions are favorable.”
VERSATILITY IS THE NAME OF THE GAME IN OUR INDUSTRY.
This new concept was also a challenge for the Boskalis crew. You used our in-house simulators?
Gerben: “Yes indeed. This was an adventurous challenge: some of the crew on board had no experience with this type of offshore heavy lifting. Boskalis designed the in-house Bokalift 1 simulator, which allows us to train in a team of four – the DP operator, crane operator, anti-heeling operator and lifting supervisor. It is also a perfect facility for simulating projects in the future.”
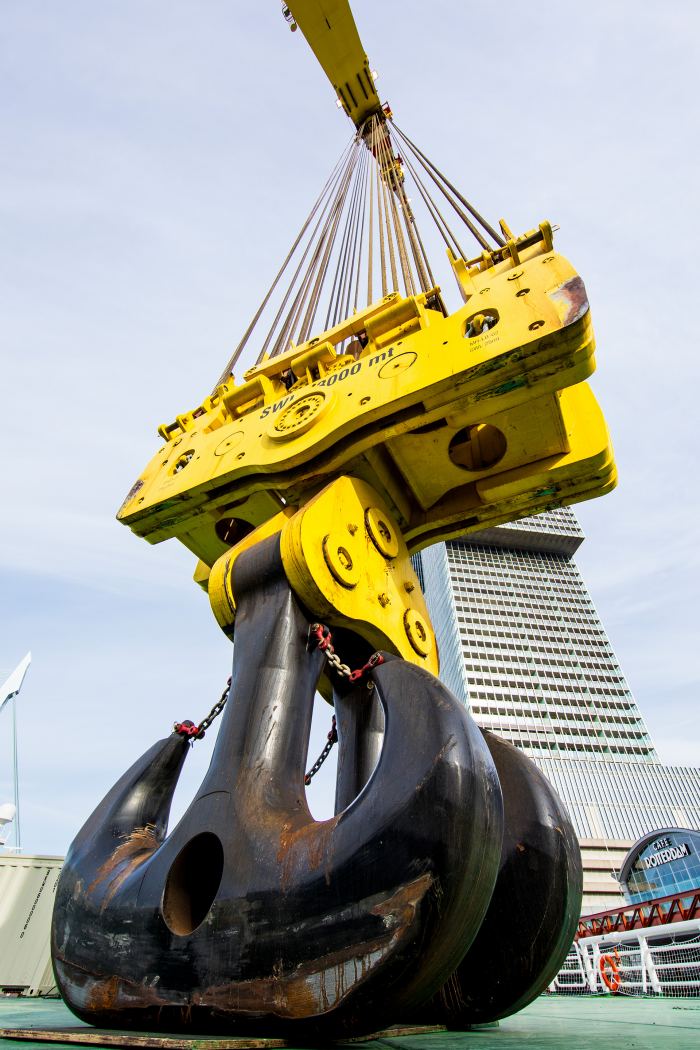
“We really want to have a dedicated crew: it’s important to create a bond with the vessel and each other. Ultimately, the people on board make the difference. This is a new concept for Boskalis. The DP2 system has to maintain the vessel’s position and heading, while compensating for the additional forces generated by the crane. We have the deck space and anti-heeling system but everything must work together flawlessly. And that means you need highly skilled people who can rely on each other!”
“We are all eager to play a role in making the concept work and live up to the expectations of Boskalis and our clients. We are already experiencing at East Anglia ONE that the Bokalift 1 is making a difference with the efficient execution of a complex installation job.”