With a total installed power of almost 24,000 kW, a total pumping capacity of 15,600 kW and a maximum cutter power of 7,000 kW, the self-propelled cutter suction dredger Helios is one of the most powerful dredgers of its kind in the world. She can dredge extra hard soils and operate in shallow waters. Meet our new mega CSD.
Helios — one of the most powerful cutter suction dredgers on the planet — marks a milestone in Boskalis’ history. Marcel van Wijk, Senior Project Engineer and André Klop, Project Manager, reveal how our engineering and newbuild teams tackled this mammoth project.
“For a mechanical engineer this project was like being a kid in a candy store” in your words Marcel — what makes the Helios so special?
Marcel: “For the Helios, we had the opportunity to come up with creative ideas and innovative solutions in almost every area. One of the most impressive aspects of the Helios is the enormous pumping capacity. The vessel has 15.6 MW to pump the dredged material through a floating pipeline to the shore. That produces incredible pressure. When dredging sand, the Helios can pump the mixture over an exceptionally long distance using its own power.”
“The wonderful thing about building a complex, advanced dredging vessel like the Helios is that you work with a large group of specialists with the aim of perfecting everything on the vessel. A cutter suction dredger is a combination of separate elements that need to be in perfect harmony. I sometimes compare it to the musicians and their instruments in an orchestra. Everything has to work together perfectly to produce wonderful music and an excellent result. During the sea trials, we took all the engines and systems to the maximum, and went to the limit in every respect. It was like a symphony! It’s a huge kick when everything we have thought up actually works in practice.”
How does the whole design and building process start?
Marcel: “For me, the process began more than four years ago. We spent the first six months evaluating the merits and shortcomings of our other cutter suction dredgers, and listing the wishes and requirements for the new vessel. That was followed by an intensive engineering process that took almost two years: formulating ideas, extensive discussions with one another, and talking to the shipbuilder Royal IHC about the possibilities.”
André: “The Helios is designed by a diverse team of Boskalis specialists. It is worth noting that eventually we processed 20,000 documents and drawings! We reviewed the drawings (mechanical, steelwork, outfitting aspects) in 3D in real time, made remarks and updated them. And sometimes this was challenging, especially when we were already building.”
One of the most impressive aspects of the Helios is the enormous pumping capacity.
Were all the designs produced in 3D?
Marcel: “Yes, an interesting aspect of the design phase was that we produced all the designs in 3D starting on day one. That is a much faster and more reliable approach. We literally modeled every part of the ship in 3D and worked out all the ideas like that, and so it was possible to calculate the different alternatives and modifications very quickly and to immediately identify possible difficulties.”
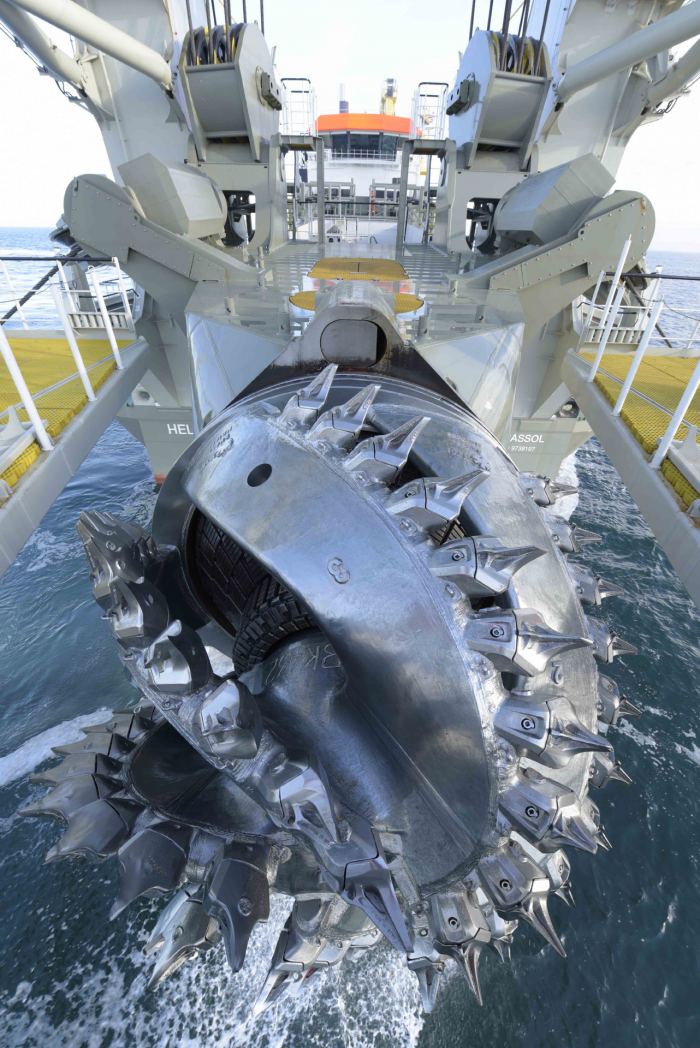
The impressive cutter head with pick points
André you led the construction work at the shipyard in Pula, Croatia and at Royal IHC in the Netherlands, what differentiates this cutter dredger from others in the market?
André: “Boskalis already has three large cutter suction dredgers in its fleet but this one has more installed power and pumping capacity, and can dredge up to 35 meters deep. She is ultra-modern, and rather than having diesel direct driven pumps all the main consumers such as the propulsion, cutter drive and dredge pumps are driven by frequency controlled, electronically powered motors. Her sheer pumping capability and efficiency is outstanding.”
Helios has a very special hull?
André: “She is 152 meters in length and has a tapered hull with a width at the fore end of 26 meters and 28 meters at the aft. The hull is designed to compensate for the heavy weight of the cutter ladder at the aft side of the vessel.”
“The hull shape in combination with her 7,000 kW cutting power, a cutter ladder of more than 2,000 tons and 150 ton pulling force side winches make her a much more efficient piece of dredging equipment. This allows us to dredge in very shallow waters. The Helios is able to dredge between 6 to 35 meters, whereas most of our competitors require a minimum of 7 meters of water.”
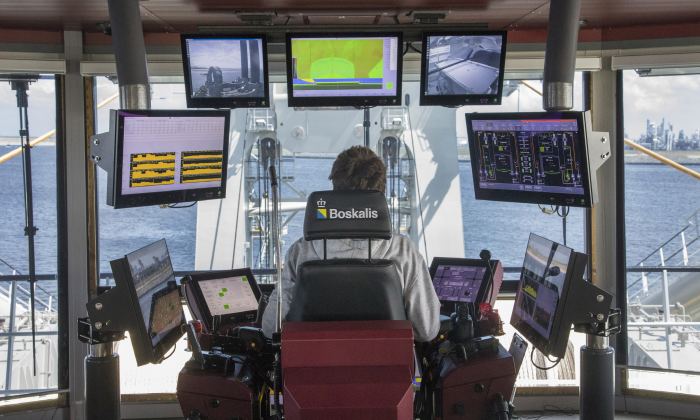
The operator controls all parts of the dredging process with two joysticks and a large number of touch screens
Safety is always paramount of course?
André: “The whole design phase was carried out within the Boskalis No Injuries No Accidents (NINA) program. We were insistent that any engineering step taken by ourselves or the shipyard Royal IHC had to have safety in mind first and foremost.”
“Additionally she has much better capacity to survive in the event of an incident. More watertight doors have been introduced. In the past if there was damage, the dredgers can stay afloat with one compartment flooded but now the Helios remains afloat even if three are damaged.”
She is ultra-modern, and rather than having diesel direct driven pumps all the main consumers such as the propulsion, cutter drive and dredge pumps are driven by frequency controlled, electronically powered motors.
Can you describe some remarkable features of the vessel?
André: “The Helios has a cutter ladder that weighs 2,000 tons – the heaviest of its kind in the world – enabling her to dredge extremely hard rocks. This ultimately lowers the cost per cubic meter of dredged rock for our customers considerably”
Marcel: “The Helios has 50-meter-long spuds, an ingenious structure of the spud carriage and we also developed a larger type of cutter head for this vessel to allow for more pick points. The Helios’ largest cutter head consists of 90 pick points. The heaviest pick points weigh 29 kilos each. We designed a new approach to make the switching of pick points during operations safer and easier. The cutter platform has been redesigned to increase safety. The platform has also been fitted out with an advanced flexible grab arm. This crane structure resembles the equipment used to change wheels during Formula 1 pit stops! We also developed an efficient approach for recycling the pick points.”
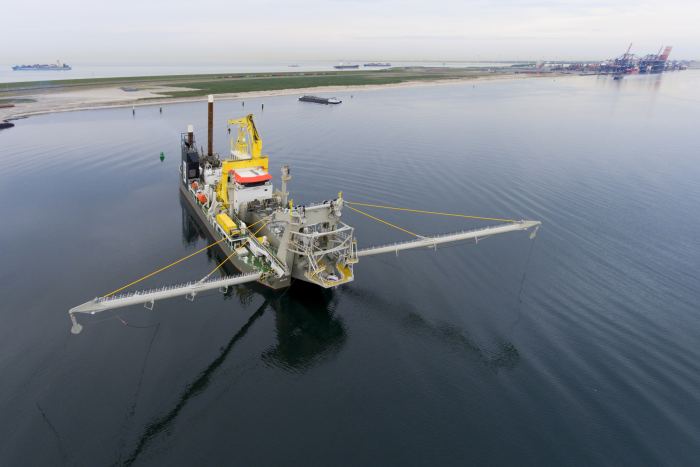
The operator’s chair is also not the usual — perhaps something gamers would be more familiar with?
Marcel: “The traditional dredging panel with dozens of buttons and meters has been almost completely digitalized. All parts of the dredging process are controlled from an ergonomic chair with two joysticks and a large number of touchscreens. The setup is like a computer game. A diverse group of colleagues, under the guidance of our colleague Vincent Jutten from our in-house Electrical and Instrumentation department, determined the best positions for the screens using virtual reality technology. Left-handed colleagues can make the appropriate adjustments. This is the first dredging vessel in the world to be controlled in this way. We are now working on a simulator setup that will allow future crew members to practice with the technology.”
Once commissioned, the Helios went straight to work?
André: “Yes, the naming ceremony was last July and in August she went straight to her first assignment executing dredging work in the Port of Rotterdam for the development of the Offshore Center on Maasvlakte 2 that will become a new port area for offshore companies. This all went smoothly and eventually she dredged some 1.5 million cubic meters of material in just three weeks. This was soon followed by the sizable dredging project for the development of the port of Duqm in Oman.”
Boskalis is clearly pleased with her performance as it has already commissioned a ‘second Helios’, is that right?
André: “Work on ‘Helios number 2’ will start soon and is expected to be commissioned and delivered in the course of 2020.”